A Deep Dive into Springs: Types, Applications, and Selection Guide Introduction to Springs
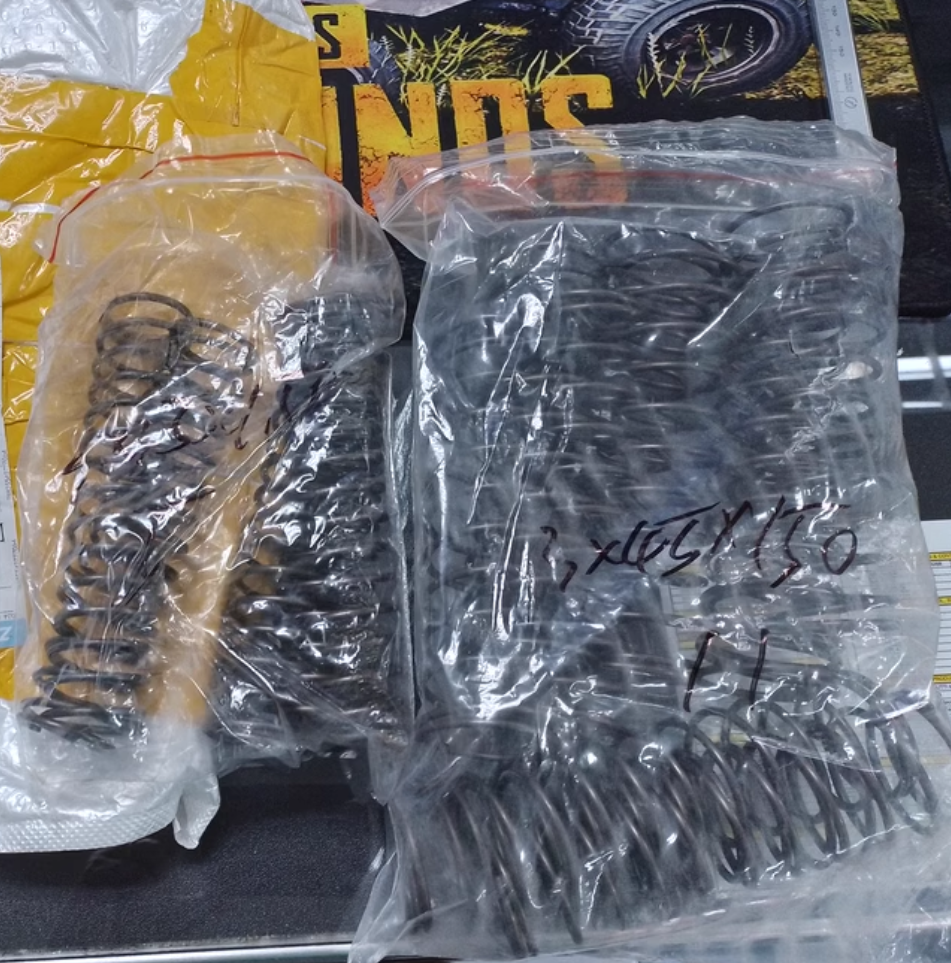
A Deep Dive into Springs: Types, Applications, and Selection Guide Introduction to Springs A spring is a commonly used mechanical component known for its unique elastic properties. It stores and releases energy through deformation and plays a crucial role in various industries. The basic principle behind a spring is its ability to store and release energy by undergoing elastic deformation, which helps regulate mechanical behavior in various systems. Springs come in various forms, including compression springs, tension springs, torsion springs, and other specialized types. The design and material selection of a spring must take into account the specific requirements of its intended application to ensure optimal performance and durability. Common Types of Springs and Their Applications Compression SpringsCompression springs are one of the most widely used types of springs. They are designed to bear compressive forces and store energy when compressed, returning to their original shape once the external force is removed. Compression springs are commonly found in automotive suspension systems, office equipment (such as chair springs), and mechanical transmission devices. In industries such as automation and mechanical manufacturing, compression springs play an essential role in ensuring stability and precision. Application Examples: Automotive Suspension Systems: Compression springs absorb shocks from uneven road surfaces to ensure smooth driving. Pneumatic Tools: In pneumatic tools, compression springs help control air pressure and manage the tool’s start and stop functions. Tension SpringsTension springs are designed to handle tensile forces. They are typically made of coiled metal wire and are known for their high tensile strength and elasticity. Tension springs are used in a wide range of applications, such as door closing mechanisms, spring scales, mechanical arms, and toys, particularly in devices that require components to return to their original position after being stretched. Application Examples: Door Closing Mechanisms: Tension springs are commonly used in automatic doors and curtain systems to control pulling forces. Spring Scales: Tension springs are utilized in spring scales to accurately measure forces or weight. Torsion SpringsTorsion springs store energy by twisting, making them suitable for applications that require rotational movement. They are commonly used in mechanical devices and tools, where they facilitate start-stop control and torque transmission. Torsion springs are essential in many precision instruments and devices, including watches, automatic door locks, and spring motors. Application Examples: Mechanical Watches: Torsion springs are the core component of the mechanical watch’s power system, providing long-lasting energy. Automatic Door Locks: In many automatic door locks, torsion springs provide the necessary torque for locking and unlocking functions. Specialized Types of SpringsApart from the commonly used types, there are specialized springs such as gas springs and constant force springs, each designed for specific applications. Gas springs are widely used in automotive, furniture, and aerospace industries for their efficient mechanical properties and durability. Constant force springs are commonly employed in applications that require a constant force output, such as reset springs. Spring Design and Manufacturing Principles The design of a spring requires consideration of several factors, including mechanical properties, material selection, size design, load capacity, and working environment. The manufacturing principles involve knowledge of elasticity, material science, and processing technologies. Common design principles include: Hooke’s Law: Describes the linear relationship between the force exerted by a spring and its displacement within the elastic limit. Hooke’s Law is mathematically expressed as F = kx, where F is the force, k is the spring constant, and x is the displacement. Fatigue Life and Stress Analysis: Springs undergo fatigue stress over time, so designing for long-lasting reliability is essential. Appropriate stress analysis ensures the spring performs well over its expected life cycle. Material Selection: The material chosen for a spring determines its strength, elasticity, corrosion resistance, and other key properties. Common materials include carbon steel (e.g., SAE 1060, SAE 1070), stainless steel (e.g., AISI 302, AISI 304), and alloy steels (e.g., music wire). How to Choose the Right Spring When selecting a spring, several critical factors should be considered: Material Selection: Choose materials that suit the working environment and load requirements. Common spring materials include carbon steel (e.g., SAE 1060, SAE 1070), stainless steel (e.g., AISI 302, AISI 304), and alloy steels (e.g., music wire). Different materials are selected based on their ability to withstand various loads, corrosion resistance, and temperature extremes. Size and Specifications: Clearly define the required spring dimensions, such as wire diameter, inner and outer diameter, free length, and pitch. Additionally, the shape and structure of the spring (e.g., spiral or flat) must be chosen according to the specific application. Load Requirements and Spring Constant: Based on the forces the spring will need to handle, choose a spring with the appropriate spring constant (k-value) and strength. Select the spring type and dimensions that match the required deformation and load capacity. Working Environment: The environment in which the spring will be used affects its performance and longevity. For example, springs used in high-temperature, high-humidity, or chemically corrosive environments require special materials, such as high-temperature steels or corrosion-resistant alloys. Quality Control: A high-quality spring manufacturer will implement a rigorous quality control system to ensure every spring meets design specifications and performs reliably. Standardized manufacturing processes and strict testing methods are key to ensuring product quality. Conclusion Springs, as essential mechanical components, play a crucial role in daily life as well as in industrial production, scientific research, and advanced equipment manufacturing. From the traditional compression spring to the more complex torsion spring, each type of spring has its unique application value. When choosing a spring, carefully considering factors such as material, size, load, and working environment will ensure optimal performance and a longer service life. As a professional spring manufacturer, we offer a wide range of spring products and custom solutions to help our clients select the most suitable springs for their specific needs. For more information or to purchase springs, visit our online store and get expert support.
Applicable Scenarios For Torsion Springs
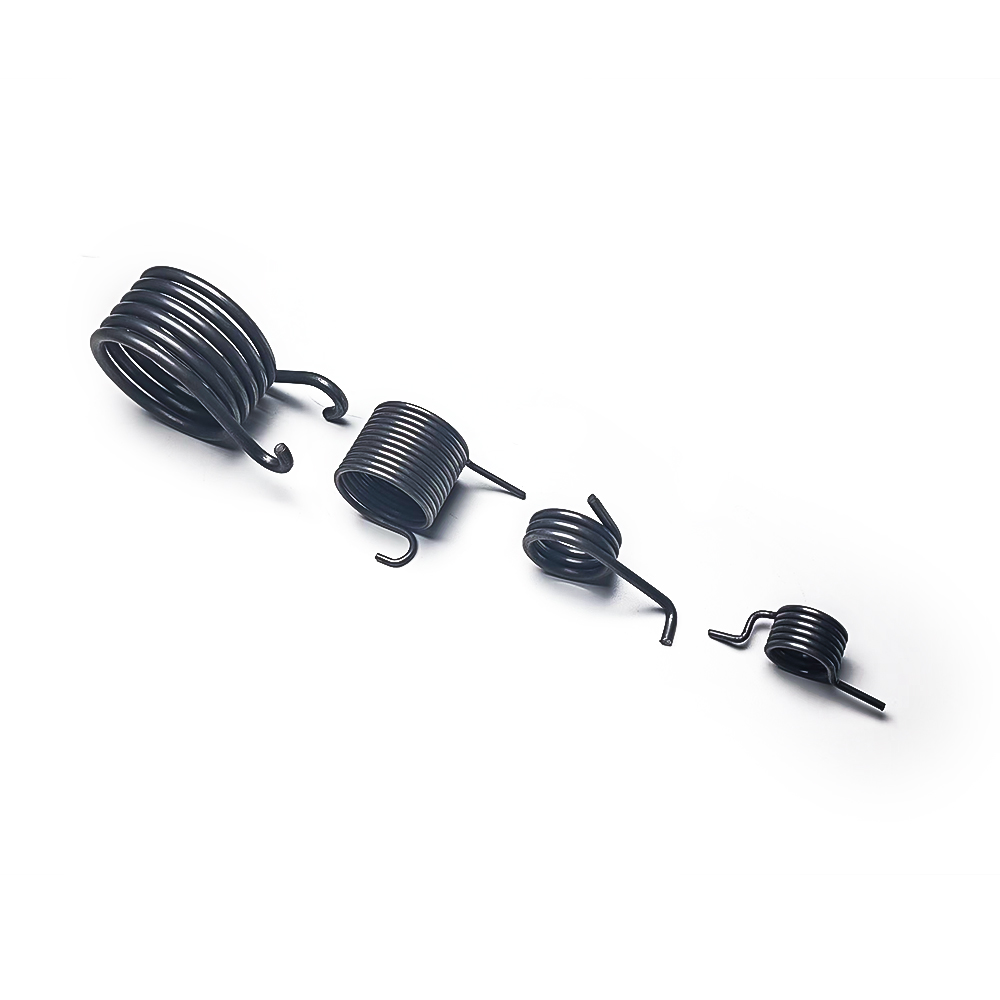
Service Details Torsion springs Applicable scenarios for torsion springs Torsion springs are the components that upon twisting, exert a force in the opposite direction. This force is directly proportional to the twisting. When twisted, these springs store mechanical energy. When released, these springs come back to their original position. The torsion springs are helical shaped springs that are capable of producing torsional or rotational forces. Based on the application for which they are used, these springs are either clockwise or anti-clockwise wound. Thus, depending on its use, these springs have a capability to work in both the directions. Where are the torsion springs used? Read the post to find out the uses of torsion springs in different applications. Top 5 Applications of Torsion Springs There are a number of applications, where torsion springs find their use. Here are some of the major areas of its application: Clocks: Torsion springs are used in torsion pendulum clocks. In such clocks, a torsion spring is used to suspend a wheel-shaped weight from the center of the clock. As the weight rotates around its axis, it twists the spring. As per its nature, the spring exerts an equal opposite force on the wheel and makes it twist in the other direction. Thus, there is a continuous back and forth motion of the pendulum, which makes the clock work by driving the gears to which it is attached. Clothes Pins: This is one of the most common applications of these springs. The working of clothes pins is facilitated by the torsion springs. These springs provide an excellent clamping action, which is why they are used in this application. Automotive: Torsion springs are known for providing even tension, along with smooth and frictionless motion. This is the reason why these springs are widely used in the automotive industry for various parts such as a vehicle suspension system, chassis, automotive valves, clutches, and gear shifters. These springs are made from materials like chrome silicone, which makes it resistant to environmental abuse, along with providing it additional strength. Medical Equipment: In the medical industry, the torsion springs are used in a number of complex equipment. Different medical equipment that make use of these springs include medical immobilization devices, hospital beds, several dental applications, wheelchair lifts and many more. For additional strength, these springs are made from high carbon steel, which also helps increase the life span of the spring. Door Hinges: These springs are widely used in different types of door hinges. Right from automobile doors and residential doors to heavy duty doors at warehouses, torsion springs are used in the hinges. These springs allow the door to come back to its original position. You must have noticed the doors in saloons that move back and forth when opened, but ultimately become stationary at their original position. This is due to the springs used in their hinges.
Introduction And Working Principle Of Compression Spring
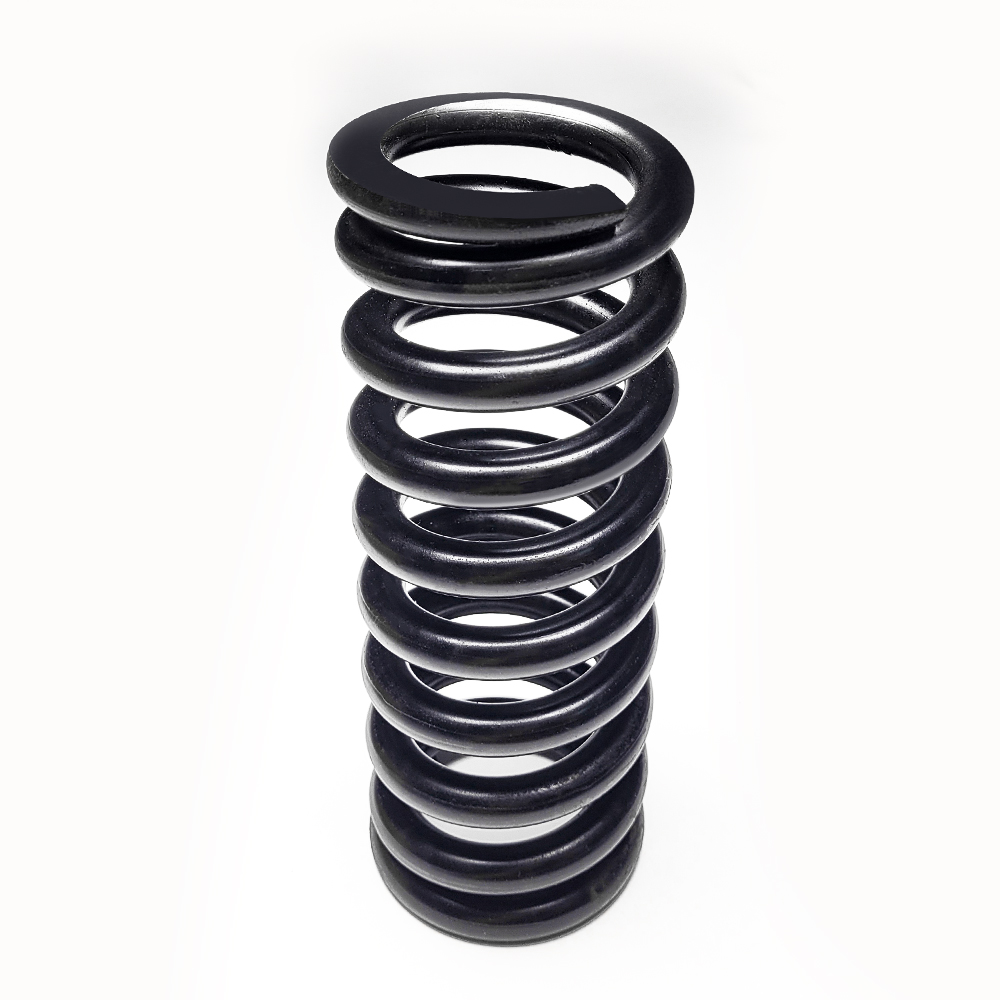
compression spring Introduction and working principle of compression spring Compression Springs are open-coil helical springs wound or constructed to oppose compression along the axis of wind. Helical Compression is the most common metal spring configuration. These coil springs can work independently, though often assembled over a guide rod or fitted inside a hole. When you put a load on a compression coil spring, making it shorter, it pushes back against the load and tries to get back to its original length. Compression springs offer resistance to linear compressing forces (push), and are in fact one of the most efficient energy storage devices available. The amount of energy stored in a compression spring is determined by the spring’s material properties, wire diameter, and number of coils. The spring’s rate, or stiffness, is determined by the wire diameter and the number of coils. The spring’s rate is the change in force per unit change in length, and it is measured in pounds per inch or newtons per millimeter. The spring’s rate can be adjusted by varying the wire diameter or the number of coils. Compression Spring Applications Compression Springs are found in a wide variety of applications ranging from automotive engines and large stamping presses to major appliances and lawn mowers to medical devices, cell phones, electronics and sensitive instrumentation devices. The most basic installation is anywhere requiring a push button. Conical type springs are generally used in applications requiring low solid height and increased resistance to surging. Key Compression Spring Parameters Rate: Spring rate is the change in load per unit deflection in pounds per inch (lbs/in) or Newtons per millimeter (N/mm). Stress: The dimensions, along with the load and deflection requirements, determine the stresses in the spring. When a compression spring is loaded, the coiled wire is stressed in torsion. The stress is greatest at the surface of the wire; as the spring is deflected, the load varies, causing a range of operating stress. Stress and stress range govern the life of the spring. The wider the operating stress range, the lower the maximum stress must be to obtain comparable life. Relatively high stresses may be used when the operating stress range is narrow or if the spring is subjected to static loads only. Outside Diameter: The diameter of the cylindrical envelope formed by the outside surface of the coils of a spring. Hole Diameter: This is a measurement of the space where you would insert a compression spring. It is the diameter of a mating part to a compression spring and often commonly mistaken for a dimension of the spring itself. The hole diameter should be designed larger than your compression spring’s outside diameter factoring tolerance and spring expansion under load. Rod Diameter: This is a measurement of the rod that goes through the inside of a compression spring. Essentially a mating part, this rod can work as a guide shaft to minimize spring buckling under load. The rod diameter should be designed smaller than your compression spring’s inside diameter factoring tolerance; however, not too small or else it loses ability to minimize spring buckling. Free Length: The length of a spring when it is not loaded. NOTE: In the case of extension springs, this may include the anchor ends. Wire Diameter: This is a size measurement of the raw material used to form a spring. Conventional springs are made with round wires that are specified to a diameter. Consult our guide on How to Measure a Compression Spring. Solid Height: This is a length dimension of a compression spring at its maximum loaded condition. Effectively, this is the compression spring’s height when all the coils are pressed together. Spring Set: This is an occurrence when a spring is loaded beyond its material elastic strength. It is a kind of permanent deformation that is noticeable when a spring does not return to its original length after releasing a deflection load. Depending on the application, spring set can be either desirable or undesirable. Load at Solid Height: This is a measurement of the force required to completely deflect a compression spring to where the coils are fully pressed together. For product designers that want to avoid the occurrence of bottoming out a compression spring, Load at Solid Height is quick reference property to find springs capable of handling an assembly’s maximum operating load. Resources
Stainless Steel Grades: All About 304

Stainless Steel Grades: All About 304 Steel is one of the most widely used materials in the world, useful for creating an infinite variety of different structures and components. Primarily composed of carbon and iron, steel can be further alloyed with a range of other elements to create a vast family of steel types. One of these elements is chromium: when chromium is added to steel, it results in stainless steel. Within the stainless steel family, there are numerous different types and grades. By far the most common grade is 304, which accounts for more than 50% of the stainless steel used around the world. 304 grade stainless steel is austenitic, a term which relates to its molecular structure and signifies that nickel has been added to the alloy. Austenitic stainless steels are the most common; as much as 70% of commercially-produced stainless steel is of the austenitic type. Stainless steel of grade 304 is composed primarily of iron, which makes up between 66% and 75% of its composition. Also included in the alloying mix is between 18% and 20% chromium and between 8% and 10.5% nickel. With a density measured at around eight grams per cubic centimetre, 304 stainless steel may also contain trace amount of other elements like silicon, sulphur , phosphorus and manganese. As standard, 304 stainless steel has around 0.08% carbon content. 304H grade has a higher carbon content of up to 0.1% while 304L has a lower amount of carbon at around 0.03%. As higher carbon content improves the strength of stainless steel, 304H is widely used in high-temperature applications. 304L, with its lower carbon content, displays increased ductility and so is often used for welding components. Austenitic stainless steels like 304 have a yield strength that represents a comparatively low proportion of its tensile strength: between 40% and 45%. Its yield strength can be further improved when the material is cold-worked. This is particularly useful when making things like spring wire. Salient qualites of 304 grade stainless steel include: Good corrosion resistance No magnetism when the metal is annealed An ability to be work-hardened Exceptional ductility and weldability High level of hygiene Ease of cleaning Good performance at both high and low temperatures Share the Post: Related Posts