스테인리스 스틸과 탄소강 압축 스프링 중 선택하는 방법
When designing high-performance mechanical or electronic systems, the choice of spring material is not just technical—it’s strategic. Stainless steel and carbon steel are two of the most commonly used materials for compression springs, but each offers distinct advantages depending on your specific application.
This article compares both materials from multiple angles—corrosion resistance, mechanical properties, lifecycle cost, maintenance, and real-world applications—to help you select the optimal solution for your industrial or electronic product.

Overview of the Materials
Stainless Steel Compression Springs are typically made from grades like 302, 316, or 17-7PH. These alloys are corrosion-resistant and suitable for environments involving moisture, chemicals, or high hygiene requirements.
Carbon Steel Compression Springs are often formed from high-carbon materials like music wire or oil-tempered 65Mn. These offer high strength and elasticity but require protective coatings when exposed to humidity or chemicals.
Multi-Angle Comparison: Stainless Steel vs Carbon Steel
Factor | 스테인리스 스틸 | 탄소강 |
---|---|---|
Corrosion Resistance | Excellent — Ideal for wet or chemical-rich environments | Low — Needs plating (zinc, phosphate, epoxy) for protection |
Elastic Performance | Good, with steady performance across moderate loads | Superior — High tensile strength and sharp snapback |
Thermal Resistance | Stable up to 250–300°C (higher for some grades) | Moderate — Degrades faster at high temperatures |
Cost & Manufacturing | Higher initial material and processing cost | Lower cost, easier to form and source in bulk |
Maintenance Needs | Low — Minimal rusting or degradation over time | Moderate — Needs protective finish and periodic checks |
Finish Appearance | Smooth, shiny surface; often no additional treatment needed | Matte finish; often dark or plated depending on use |
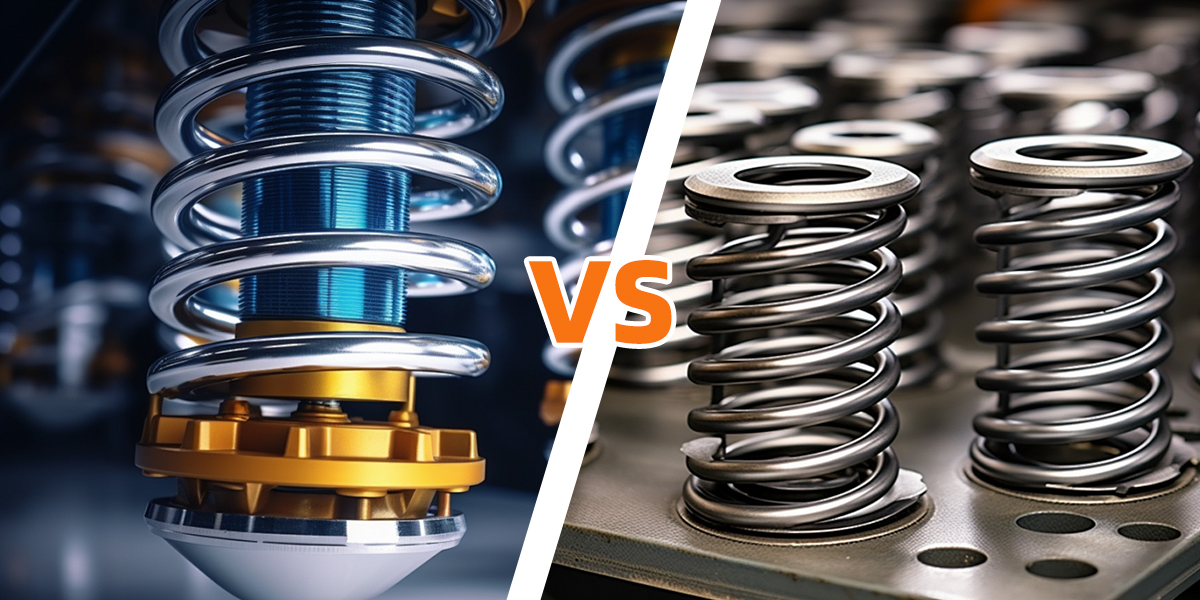
Application-Based Selection
Ideal Use Cases for Stainless Steel Springs
- Outdoor machinery exposed to rain, salt, or UV (e.g., agricultural drones)
- Medical devices and surgical tools requiring sterilization
- Food-grade equipment with hygiene and corrosion regulations
- Electronics used in humid environments (e.g., smart home sensors)
Ideal Use Cases for Carbon Steel Springs
- Enclosed machinery in factories or labs
- Consumer electronics requiring high elasticity but minimal exposure
- Automotive interiors or tool components
- DIY devices or temporary assemblies where cost is a major factor
Performance Over Time: Which Lasts Longer?
While carbon steel may perform better under initial loads, it tends to corrode faster and lose tension more rapidly if used in damp or corrosive environments. Stainless steel, though more expensive, offers long-term stability and often lowers the total cost of ownership by reducing failures, replacements, and maintenance downtime.

Frequently Asked Questions (FAQ)
1. Can carbon steel springs be used outdoors?
Technically yes, but they must be coated with a protective finish (zinc, powder coat, epoxy). Without it, carbon steel will rust quickly in outdoor conditions.
2. Is stainless steel always better?
Not always. In dry, enclosed environments, carbon steel often outperforms in elasticity and cost efficiency. Stainless shines where corrosion and reliability are key concerns.
3. Which material is more eco-friendly?
Stainless steel is 100% recyclable and often has a longer lifespan, reducing waste. Carbon steel is also recyclable but tends to have higher maintenance and replacement cycles.
Next Steps: Find the Right Compression Spring
Choosing the right spring material goes beyond specs. It’s about understanding your product’s real-world conditions. Explore our compression spring collection to view available options or contact our team for a personalized recommendation.
Have questions or want to request a custom spring? Contact us today — our engineers are ready to help.