Springs are essential components used in many industries, from industrial machinery to consumer electronics. However, the process of making these springs involves several steps, and each step is crucial to ensuring the final product’s quality. The journey begins with the selection of the right material. Steel wire, which is often chosen for its strength and flexibility, is carefully selected. This material will eventually be shaped into compression, torsion, or tension springs, depending on the application. Learn more about compression springs here.
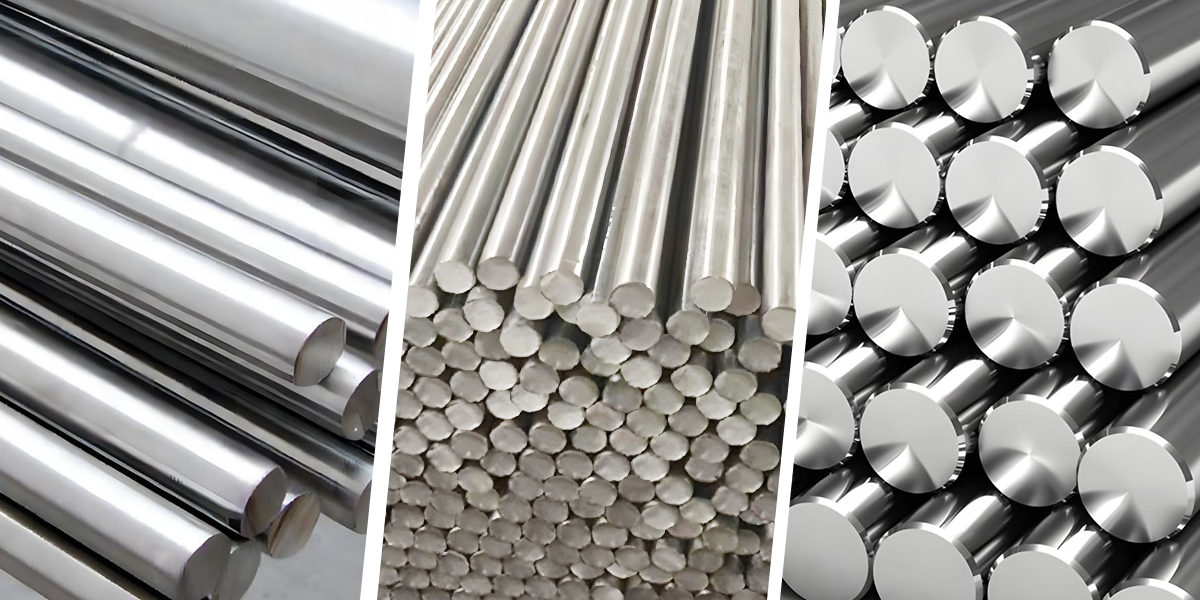
1. Choosing the Right Material: The Foundation of a Spring
The selection of the right material is one of the most important steps. High-carbon steel, alloy steel, and stainless steel are commonly used. Each material has its unique properties, which will affect the spring’s strength, corrosion resistance, and elasticity. For example, high-carbon steel is often selected for general-purpose springs due to its durability. Stainless steel, on the other hand, is preferred when resistance to corrosion is required. These materials are thoroughly tested before they are used in the manufacturing process.
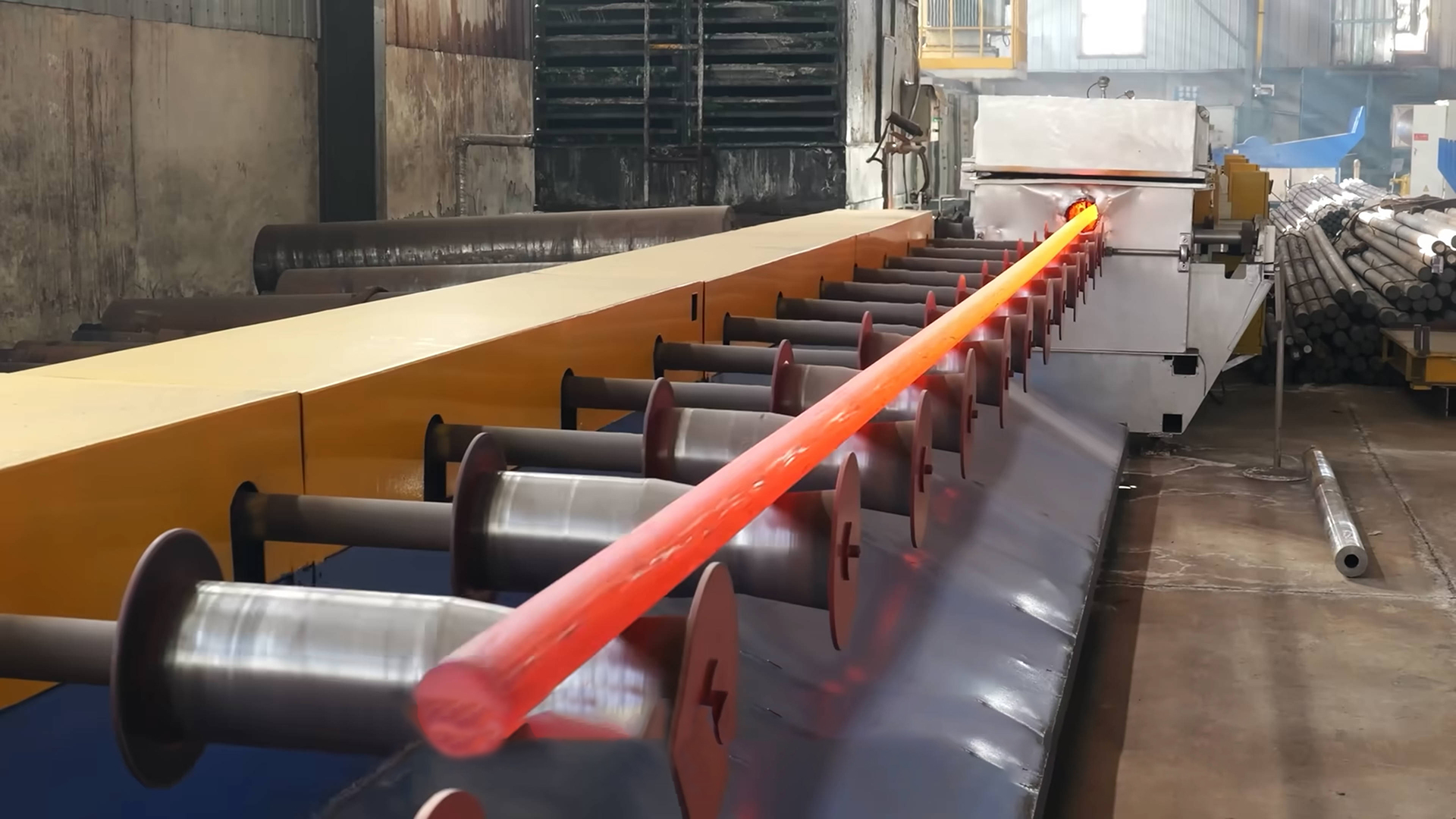
2. Drawing the Steel Wire: Cold and Hot Drawing Methods
Once the material is selected, the wire is drawn into shape. This process can either be done cold or hot, depending on the wire’s intended use. Cold drawing is typically used for smaller diameter wires, as it enhances the material’s strength. In contrast, hot drawing is used for larger diameter wires and allows for easier shaping. Both methods result in wire that is ready for coiling into the desired spring form.
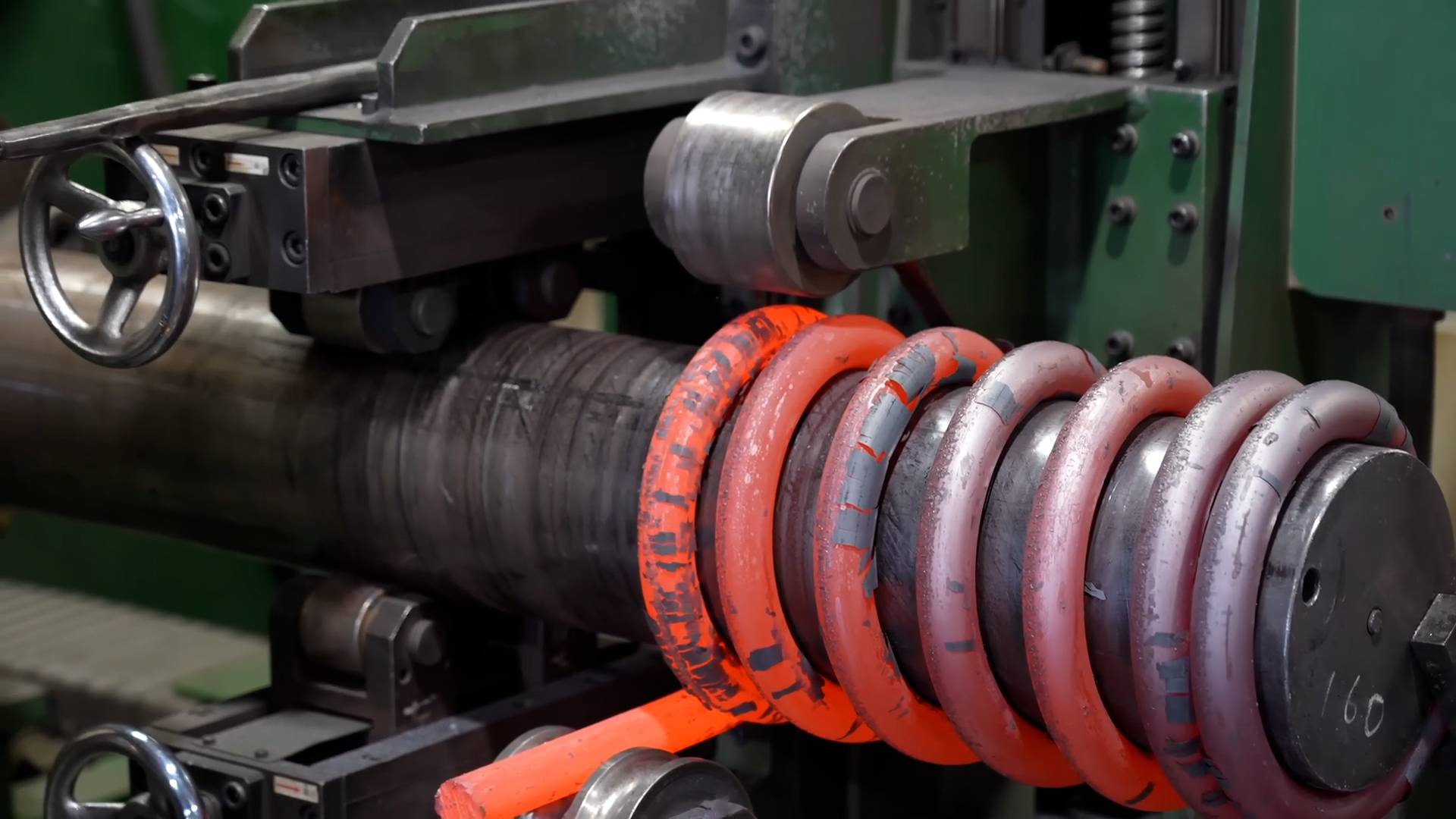
3. Forming the Spring: Coiling or Bending
After the wire has been drawn, it is then coiled into the desired shape. The wire can be coiled into several types of springs, including compression, torsion, and tension springs. For compression springs, the wire is wound into a helix. This process is performed on a compression spring machine. Torsion springs are coiled to resist rotational forces, while tension springs are designed to resist pulling forces. Special machines are used to ensure the springs are accurately coiled.
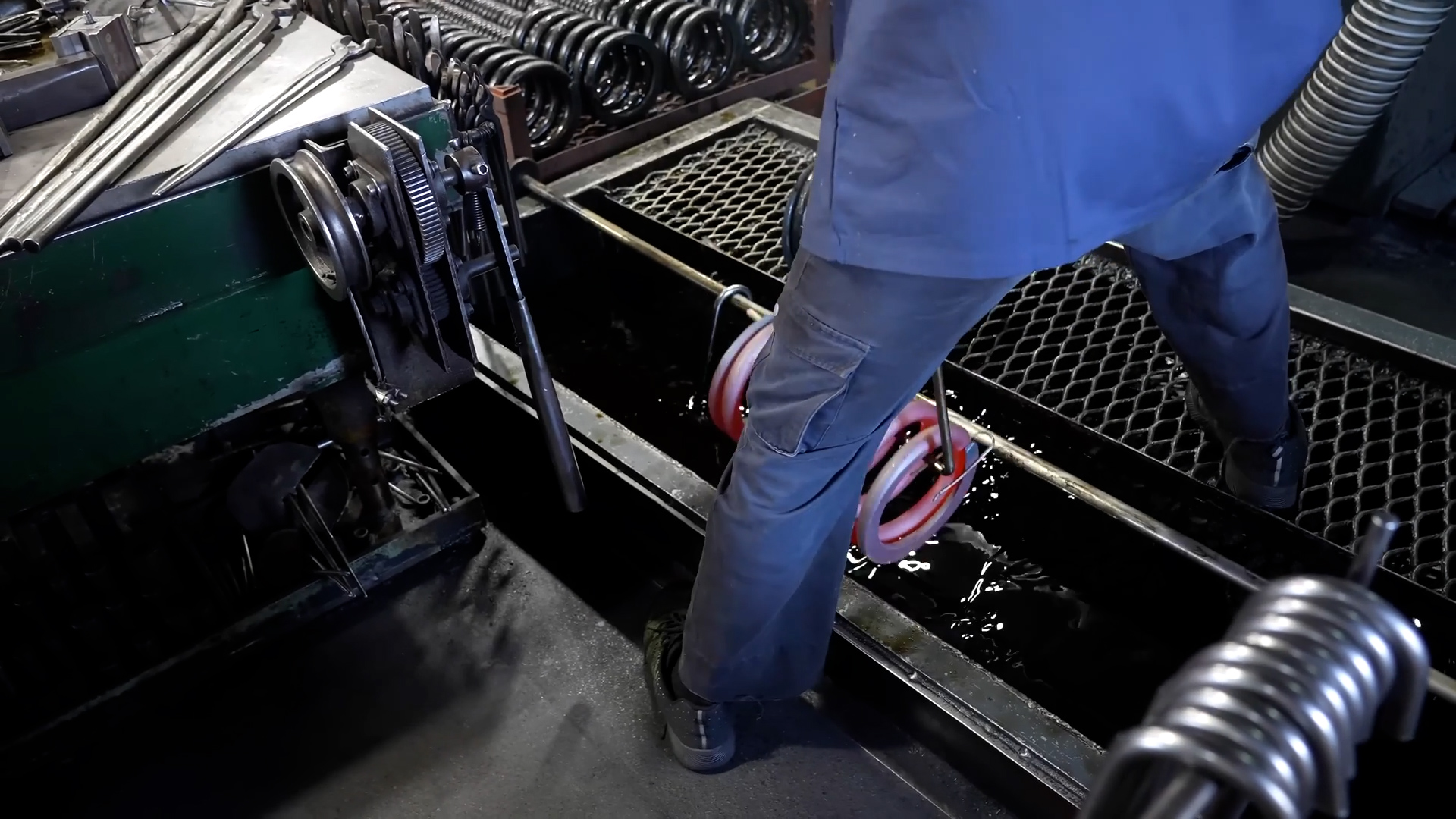
4. Heat Treatment: Strengthening the Spring
Heat treatment is used to enhance the mechanical properties of the spring. During this process, the spring is heated to a specific temperature, then cooled rapidly to harden it. Different heat treatments, such as annealing, quenching, and tempering, are employed to adjust the spring’s strength and flexibility. These processes are critical to ensuring the spring performs as expected in its final application.
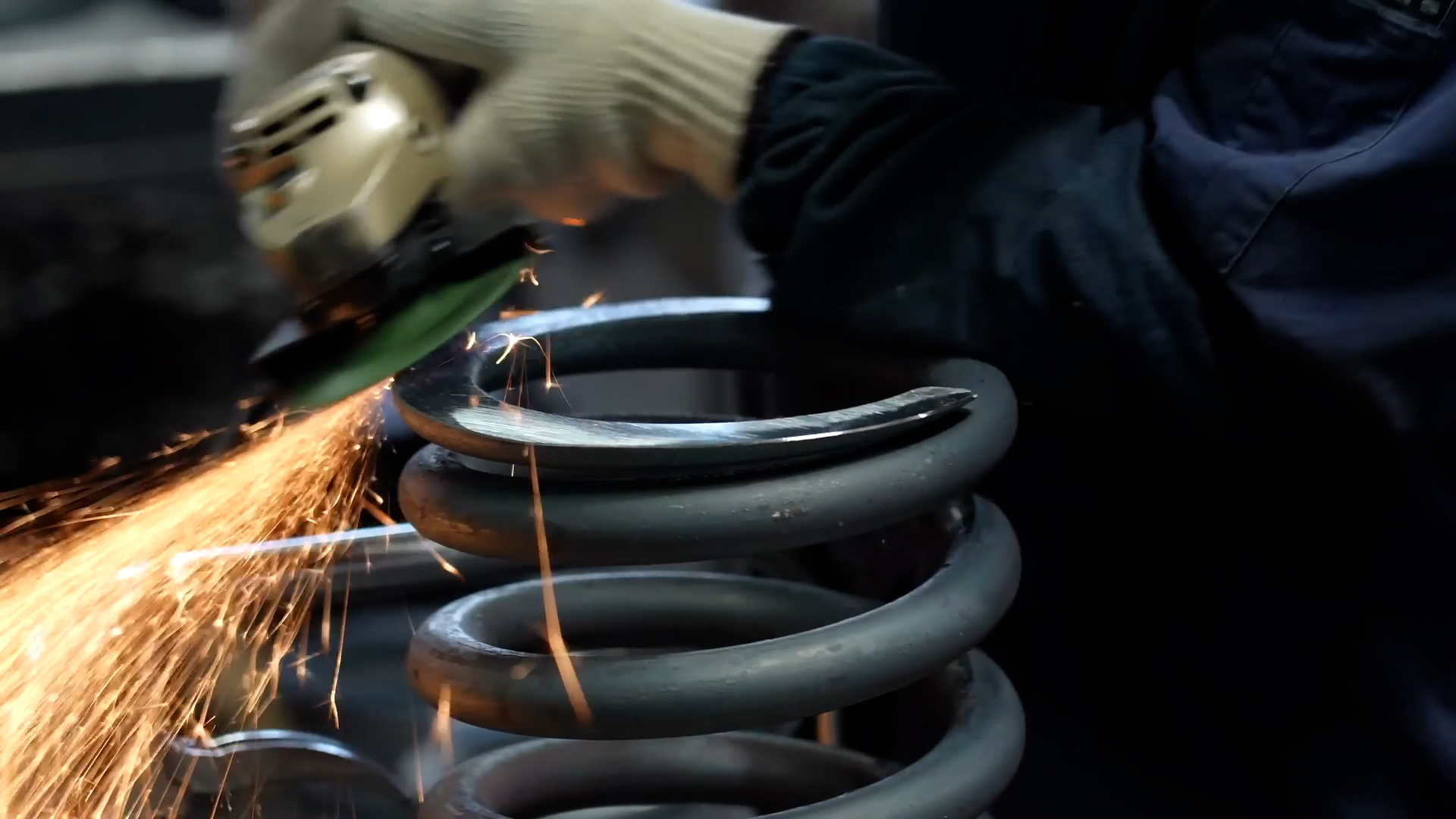
5. Precision Finishing: Ensuring Accuracy
After heat treatment, the spring undergoes a series of finishing processes. These include cutting, grinding, and polishing. The ends of the spring are ground to ensure they are flat, which is essential for proper installation. These steps ensure that the spring meets the required specifications and can function as intended in various applications. Additionally, each spring is tested for its mechanical properties to ensure its performance.
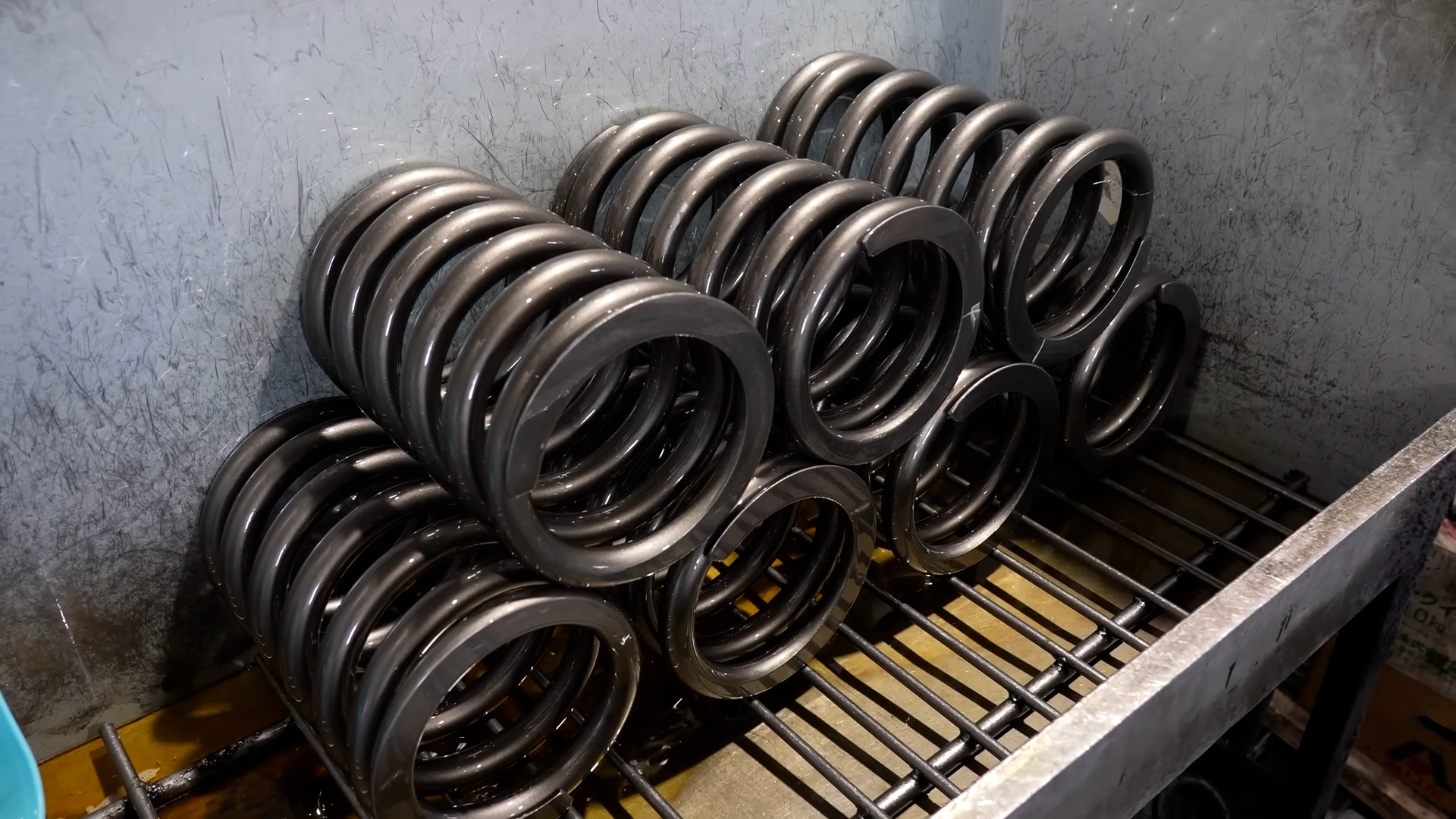
6. Surface Treatment: Enhancing Durability
In certain cases, surface treatments are applied to improve the spring’s durability. This may include electroplating, coating, or other methods. Electroplating involves applying a thin layer of metal, such as zinc or nickel, to protect the spring from corrosion. Coating methods, such as powder coating, are also used to provide additional protection against wear and corrosion. These treatments are especially important for springs used in harsh environments.
7. Quality Control: Ensuring Perfect Performance
Finally, the spring undergoes a series of rigorous tests. These tests are conducted to ensure that the spring meets the required specifications for strength, elasticity, and durability. The spring is subjected to various loads and tested for its performance over time. Springs that pass these tests are deemed ready for use in their respective applications.
8. Applications: Where Springs are Used
Springs are used in a variety of industries, from automotive to aerospace, electronics, medical devices, and more. Depending on the application, the type of spring and material chosen will vary. Compression springs are often used in mechanical assemblies, while torsion springs and tension springs are used in more specialized equipment. Custom springs are frequently designed to meet specific requirements, ensuring optimal performance in each application.
If you are interested in learning more about our custom springs or need assistance selecting the right spring for your application, contact us today.
For more information on spring manufacturing and materials, check out the detailed guide from Springer, a leading publisher in mechanical engineering.